Insulation bath: how to do?
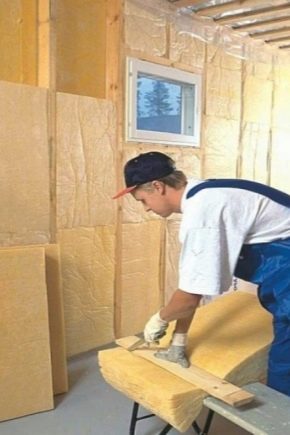
In any bath, a boiler, stove or other powerful source of heat is used for heating. But even these funds will be ineffective if you do not take care of the proper weatherization of the building.
Special features
It is necessary to warm the room of a wooden bath. Even the relatively low thermal conductivity of the wood itself does not guarantee an acceptable thermal protection. The old log constructions could simply be laid between the crowns. But the appearance of more sophisticated and practical round logs made such an approach impossible. Meanwhile, any bath should be performed as a kind of thermos, stably maintaining internal heating regardless of the temperature outside.
If the building was built of expanded clay blocks, the approach should be somewhat different.The main role in this case is played by heat protection from the inside. Heat should be saved only at the moment when the bath is heated.
The outer protective layer almost does not help in this task. Moreover, systematic temperature differences can destroy any insulating substance.
Stone blocks warm up faster and more significantly than wood, therefore wood cladding is usually placed outside, and insulation is put under it. For all the importance of thermal protection inside, the quality of its external contour cannot be ignored. It depends on how resistant the walls will be to freeze. In addition to wall planes, additional warming is required:
- ceiling;
- floor;
- foundation under it.
Quite a lot of baths are built on the basis of a cinder block, and here, too, it is necessary to decide which heat protection option will be the best. As is the case with other stone parts, it is recommended to use both the outer and the inner layer. A layer of thermal insulation is created on the floor, which is twice as thick as the main walls. Only then put the screed and made finishing. The walls are formed obreshetka with rails.The thickness of each rail is at least 5 cm; thermal protection overlaps with foiled materials that hold water.
Saving on waterproofing or external finishing of cinder blocks turns out very often with serious material losses, the inability to retain heat. Maximum attention should be paid to the preparation of air gaps. But besides slag concrete, private developers use other economical construction materials.
So, you can find dozens and hundreds of baths, built of sleepers. These are reliable and proven designs that can withstand strong mechanical loads, but they will also need to be insulated.
The gaps from one part to another are filled with mounting foam. Insulation is laid out over the first crown, and later over the next ones, as soon as a certain tier is finished and mechanically fastened. Much more often, however, than the "railway" bath, there are structures of the boards. It is possible to warm a frame design:
- mineral wool;
- fiberglass;
- polystyrene foam;
- maximum available penoizol.
The actual practical properties of these materials differ much lesswhat manufacturers are trying to show in advertising. Therefore, the focus should be devoted not to choosing the ideal solution, but to strict adherence to technology. Expanded polystyrene almost does not need waterproofing. But here the steam barrier will have to be constructed anyway. On the market, such newest thermal protection for frame structures, such as Penoizol, is taking more and more strong positions.
If you want to use the old chopped bath, there is no reason to refuse it for technical reasons. Modern technologies even allow to raise the characteristics of such buildings to a new level. It is logical to use for the felling of the most natural heaters that do not affect its environmental performance. The overwhelming majority of professional brigades in this case gives preference to basalt wool. Used for many centuries, the tow has been good at holding back drafts and preventing heat from leaving, but it serves too little.
Among the different varieties of moss is best kukushkin flax, which is immune to moisture. But any mosses are easily damaged by moths. Special treatment prevents such a development of events, only we can’t talk about the full naturalness of the coating after it.The combination of flax and jute differs in the increased service life; The disadvantage of this combination is the increased cost. But the convenience of warming and the impossibility of rotting will delight any consumer.
Work with different types of buildings
The tree has the best ratio for thermal conductivity, environmental friendliness, hygroscopicity, sanitary safety.
But even relatively low (compared to other structural materials) heat leaving to the outside is often unreasonably large for specific people. Each log or piece of coal in the furnace, each revolution of the gas (electric) meter significantly increases operating costs. It is not necessary to warm the wooden walls from the inside, because the dew point is inside, the surface temperatures will change dramatically, in addition, useful space is wasted.
To insure wood and insulation from the action of strong heat, it is recommended to put metal sheets, put a brick or apply heat-resistant drywall. Insulation is applied to the boards in a continuous layer, and the framework is first mounted on logs.
When building a bath using frame technology, thermal protection is performed using plates or mats. Rolled versions of coatings are permissible, but it is very difficult to expand them inside the frame. Until recently, basalt wool was considered an absolutely safe coating, but from 2014 it became clear that this was not the case. When heated, the adhesive mixtures used to connect the fibers may begin to release formaldehyde.
Chemists cannot say how great the danger is - studies are still under way, but at least for the steam room, it is better to use other options.
The frame bath is perfectly insulated using linen mats, which are made by simple pressing and do not contain the slightest artificial inclusions. At the same time, strong compression allows you to retain heat and stably hold the initially created structure. Creating a classic type of wall cake, the warming material is exhibited from external boards to interior decoration.
Outside, a bath, built on frame technology, can be warmed only as an auxiliary device. Typical thickness layout materials - 5 and 10 cm; for buildings that will be used year-round, you need to take the largest figure and fold in half.
From foam blocks
Warming foam walls - a fairly simple matter, and even newcomers in the field of construction will be able to cope with it. There is no need to level the plane, it is ideal at the very moment when the blocks go off the assembly line. Street insulation foam blocks produced by almost all existing materials; an exception is made for frankly inconvenient or impractical solutions. Most experts recommend putting decorative plaster on the insulation - it will not only improve the appearance, but also help enhance thermal protection. If the facial finish is made with the help of siding, you still should not rely on the air gap, and use a full insulation for the finishing strips.
The work on the insulation of the foam concrete wall is carried out simultaneously with its installation, and the first steps should be taken already when building the foundation. It is acceptable at this stage to use only those materials that tolerate excessive moisture, temperature changes and the action of soil animals, rodents and insects.
The ideal solution is foam, in addition, it is easy to install and is relatively inexpensive.Cold leaking floors in foam baths are not insulated at all. Mineral wool is most often placed on top. There, evaporation will least of all seep inside, and at the same time the level of thermal protection will be higher than that of an identical loose layer. Given the properties of foam blocks, all walls must be supplied with steam barriers.
Brick wall
Baths made of brick are solid and durable, for many decades they have been practically the benchmark, and they are still valued. But lowering the fire hazard and increasing strength in comparison with wood turns into a significant heat consumption. Internal heat protection in a brick bath is formed mainly with the help of an auxiliary wall along the main body. As an option, you can put two layers of coiled or plate insulation. Reasonable builders combine these two options.especially in areas with severe winters and strong winds.
In a brick bath, thermal protection of the floor is carried out with the help of expanded clay or polyfoam; other means are rarely used. The vertical course of base insulation using Penoplex or PU foam is not available for amateur builders, this should be done by specialists.A vapor barrier and heat insulation are laid on the subfloor, then a reinforcing mesh is exposed. Already on the grid will be easy to form a cement screed. When the drying solution is dry, it is treated with waterproofing and spread with ceramic tiles.
Device floor and selection of tools
Work on the arrangement of the floor in the bath requires the use of a variety of tools. Since in most cases they are formed of wood (this is especially important for steam rooms), you need to use the usual carpentry set. The floor can be made with a water pass in the gap or in one separate drain. This drain is directed to one side, otherwise the stability of the water drain cannot be guaranteed. If the floor is formed without ducts, under it is fixed non-removable flooring to be replaced only at the end of the working resource.
To keep the surface warmer, the gutter and the drain leading into it are placed in the lowest place. The design of removable floors implies the possibility of periodic analysis at a time when the bath is not used. When forming the screed, you will need a cement grater and special rakes, trowels and spatulas of various sizes. The evenness of the structures is provided by the level (hydraulic or laser).
Wooden floors are created with a hammer, metalworker, electric planer, screwdriver and drill.
Types of insulation and requirements for them
The indispensable requirements for any heaters will be:
- minimal hygroscopicity;
- no release of harmful substances;
- optimal heat reflection inside.
Among the high-tech developments attracts attention "Penotherm". It is difficult to call it a new option, but this is even a plus - there is already a relatively long experience of using it. As practice has shown, neither mineral coatings nor polyurethane foam can be compared with this method of thermal protection. In baths and saunas, it is used only in the form of sheets, covered outside with foil. Marking "NPP LF" shows that the basis of the material is low density polyethylene; aluminum layer helps to withstand stable heating to 170 degrees.
"LP" - a series, which is made of polypropylene in sheet format. This coating is not able to transfer temperatures above 60 degrees. Therefore, it can only be used for floors and walls in the waiting rooms, rest rooms and dressing rooms, vestibules.
The use of "Penoterm", labeled as "PE", in bath houses is unacceptable for technical reasons. Heat protection functions stably when heated to 1500 degrees, without even losing mechanical characteristics.
Any aluminum-based foil material has advantages such as:
- rapid heating of the internal volume;
- excellent thermal inertia;
- Stable steam retention.
According to statistics, up to 4/5 of the total heat is transferred indoors in the form of infrared rays. The aluminum screen becomes an impenetrable bastion for them, does not release precious thermal energy to the outside. Thanks to modern technology, the foil can be single, double or even triple in composition. The common opinion that the layer of aluminum should be completely open for normal operation is fundamentally wrong. On the contrary, if finishing materials are placed outside - the same lining, their thermal qualities noticeably increase.
What is important, the air inside the bath warms more evenly. But the foil must be glued directly onto the layer of the main insulation, because otherwise the air gap will increase the heat transfer.It is better to use a metal reflector on top of stone walls with overlapping stone wool or slab material.
It is important to remember that not every roll of special wool sold in construction markets and in stores is suitable for use in the bath. Some manufacturers go to the trick and for the sake of increasing the resistance to water, they use cheap but harmful to human health additives.
Minwat generally not afraid of fire and is considered one of the relatively safe materials. Covering it from above with foil additionally lowers even the small risk of toxin release that still remains after finishing. The coating stably transfers up to 200 cycles of heating and freezing, and even after that its replacement is not needed. The total service life can reach 30 years, and the high mechanical fortress will greatly please those who like to drill the bath walls and hang additional objects on them.
A prerequisite for the installation of wool insulation is high-quality obreshetka.
The pitch of the supporting structure is determined in such a way that the heat insulating plates enter inward freely, but at the same time they are kept rather tight.Waterproofing is performed using either a special type of foil or polyethylene with a thickness of 150-200 microns, or using penofol. In the frame baths, the waterproofing layer is made strictly of foil, and lining is placed above it. A layer of basalt wool should be 6 cm. Kraft paper can be used as a substitute for aluminum foil.
Foil can be presented in the format of folgoisolone - so called polyethylene with deposited aluminum layer. The advantage of such a coating can be considered that it guarantees excellent noise absorption and is much stronger than the usual analog. In addition, heat retention is provided not only when it is reflected, but also due to reduced permeability. The cost and environmental characteristics are primarily influenced by the insulation that is used as the basis. It also determines the resistance to aggressive effects, especially intense in the steam room.
It should be borne in mind that aluminum perfectly passes electricity. Because all the wires in the walls will have to isolate especially carefully. To make the foil surface stronger and to prepare the basis for the finishing, high-quality obreshetka will help. Allowable aluminum layer ranges from 30 to 300 microns.When using correctly calculated surface it is possible to achieve the same effect as in the construction of a thick and heavy log house.
Step-by-step instruction
It is very important to imagine how the insulation will be gradually formed from the inside with your own hands. This is useful even when ordering the services of professional builders. Very many of them, when faced with insufficient control or weak customer competence, try to choose the easiest and most profitable ways for themselves. The first step in the work, regardless of the choice of traditional or ultramodern heaters, is a thorough preparation of the surface of the walls.
If errors are made at this stage, all subsequent actions have no meaning.
It is unacceptable to put the foam in the steam compartment, it emits extremely hazardous substances. The joints of plate insulation of any kind on technology relies sizing foil tape. It will form an airtight layer with a very high level of thermal protection. Plates or rolls are recommended to put crates in the cells, which is collected from a wooden bar.The cross section of this bar is determined by how powerful the insulation should be (minus 10-20 mm from the actual value).
If you have to fill the wall with something loose, the bars are separated from each other by 0.45-0.6 m. The parts of the batten are attached to a wooden substrate using dowels or screws; when further stone, brick, concrete is located - only an anchor helps. In the first case, the depth of fasteners is enough for 20-25 mm, and they are required to enter the main walls by 40 mm at least. But to exceed the value that is justified for fixing a certain type of timber is not worth it, it is just extra expenses.
With the exception of basalt wool taped on the production of aluminum foil, all materials need reinforced insulation from moisture.
Thermal insulation on a concrete screed will require a whole range of additional elements. Be sure to need will be strengthening nets, special mixtures (ready-made or made up of primary components), which set the course of the beacons. Also, it is impossible to do without extinguishing thermal compression and expansion of the tape, without polyethylene. Whether the floor is made of wood or concrete does not matter, but under the concrete surface you need to pour a large amount of claydite. The minimum excess is 100%, but if the total height of the room and material capabilities allow, you can even exceed this figure - it will be safer.
Before warming the floor on the ground before marking is required:
- ram all the soil in the desired area;
- waterproof the walls;
- pour 0.1 m of sand, fill with water and thoroughly tamp;
- lay out roofing material with a 15 cm wall approach.
Single sheets of material are also placed with a mutual foray of 0.15 m. The connection at the joints is ensured with construction tape (which is necessarily waterproof). Placing guides on the subfloor is made in strict accordance with the layout. It is possible to fix these guides in an arbitrarily chosen way, so long as it is reliable. Trying to do without guides - frank nonsense, because even trained professionals use them.
Attic insulation is even more important than facade insulation. It is impossible to approach this work in the same way as in a regular house. Indeed, in the bath room the upper part constantly concentrates water vapor. In most cases for work use:
- mineral wool;
- glass wool;
- Styrofoam;
- clay;
- sawdust;
- a combination of moss and wood ash (only for walls and floor).
As for the foam, it should be used only in an extreme situation, when there is simply no other way to save money. The cheapest option - the use of sawdust in the cut, it also has a high environmental friendliness. Thin slats are made of timber across the boards, the distance between them is about 1 m. The vapor barrier is overlapped, the cloths are approaching about 20 mm. To obtain a suitable solution, 40-50 kg of clay is mixed with 200 liters of water; After adding sawdust, the mixture should become one consistency.
Apply such a coating with a thickness of 80-100 mm, with a little ram it. Especially carefully have to lubricate the intersection of walls and ceilings. There will inevitably arise a gap - and each of them will be filled. In a large bath, sawdust is easily replaced with expanded clay. You can also apply the garden soil or a mixture of black soil with peat in equal proportions.
Since the temperature in the washroom and the dressing room as well as in the rest room is clearly lower than in the steam room, they can be insulated with foam plastic.There it is relatively safe, although it is still worth considering an alternative solution. If the choice is made in favor of foam, it is either glued (to brick and concrete), or placed in a stuffed frame. Given the immunity of this material to water, it does not need to be covered with special films. You will only have to finish.
It is possible to surround the stove itself or the boiler; places of adjunction to other structures are allowed only with basalt wool. Has its own characteristics of insulation in the basement of the bath. The ground floor is supposed to be warmed both outside and inside. If done correctly, the total heat loss can be reduced by 10-15%. The most suitable solutions to this problem are traditional foam plastic and extruded polystyrene foam. These materials are not only minimally sensitive to water that is constantly circulating in the soil, but also resist external pressure.
But mineral wool is categorically not justified in this case. There is nothing to burn there, given the high risk of moisture destruction, you will have to make a complex waterproofing system that will absorb all the savings.When using foam, although it masks deformations up to 1 cm, it is better to correct such curvatures, so it will be more reliable. When leveling the basement of the sauna with plaster, sometimes it is necessary to apply two or three layers; each should fit only on the dried substrate.
Walls
Warming of the walls outside is extremely rarely carried out separately. After all, it will then lead to an incorrect distribution of heat in the thickness of the material. The walls, the floor and the ceiling will warm up first, and only then will the air temperature rise. This, of course, is not at all what is expected from a quality bath.
External heat protection is required if the bath room is combined with a residential house. It is logical to use it under the finishing materials, when there is an opportunity to improve the thermal quality of the building. But in the case of non-residential baths it is worth considering whether this is really so necessary. After all, even the most affordable thermal insulation is very strongly reflected in the personal budget. If the decision is made, you will definitely need layers of steam and wind protection. The design will include:
- crate;
- heat protection;
- wind insulation;
- counter lattice;
- final layer.
Formally, there is no need for a counter lattice. But any experienced craftsmen put it in order to more easily and quickly create a ventilation duct. The tree is necessarily impregnated with antiseptic. If the installation goes on a brick wall, it is advisable to use dowels, they will compensate for the excessive rigidity of the structure and speed up the installation. Foamed glass is technically perfect, but using it turns out to be too expensive.
The choice of facial finishing material is limited only by considerations of aesthetics and personal taste.
Steam room: ceiling
Baths of aerated concrete are built precisely because this material has an impressive level of thermal insulation. The design will last for a long time and will release only a small amount of heat. By this parameter, it comes close to the tree. But you still need to isolate the wall insulation in the steam room, to radically reduce the loss of expensive energy. Wood paneling turns out to be the most expensive solution for the ceiling of this room and absorbs a hefty height.
Foam glass ultimately becomes even more profitable than upholstery.In addition, it is superior to polystyrene foam (to which it looks like externally), since it does not emit toxins with significant heat. Installation of such a coating is made on tile glue, and when choosing this glue, paramount attention should be paid to its safety. The same adhesive composition will perform the role of putty. It is undesirable to apply the mixture in excess, it will still be covered with clapboard.
Heat-proofing of the steam room is often carried out with penofol. It is important to remember that it acts only as an addition to other coatings. High-quality work involves the installation of a package of polyfoam and penofola; air pause from foil to the front layer is 1.5 cm. Thanks to this gap, retention of both heat and steam is improved. Polyurethane foam will help to close the seams of the structure, and if you need to seal the intersections of the webs, use adhesive tape for this.
If the bath is built from a log, its thermal characteristics will be excellent. But this is not a reason to neglect modern technological solutions. Be sure to create a kind of "thermos", with maximum attention paid to the attic floor.That it is - the weakest link in log structures.
Before starting work, the tree is carefully inspected, problem areas are corrected and removed, treated with antiseptics.
Floor
When thermal insulation is provided, it is possible to take the base of the room. After all, even if the walls and the ceiling are quite warm, but the floors are cold, it devalues all the work done. When using penoplex for lags you need:
- lay insulation between the elements on the subfloor;
- imitate the basement (laying the lining on the perimeter);
- create vents for ventilation (each minimum is 0.05 square meters);
- put a blind area on the perimeter in order to improve the discharge in the direction of various drains and precipitation.
Some believe that it is possible to make the impregnation of wooden parts located on piles, antiseptics. But the usual types of impregnation evaporate already in the sixth or seventh year of use. Therefore, you should carefully select the mixture and give preference to compositions deeply eaten into the tree. If the bath is built on screw piles, even the most powerful floor insulation will not help ensure its normal operation. It is necessary to equip the sabot and thereby prevent over-ventilation of the underground.
Warming of the concrete floor with expanded clay is a real salvation for those who want to guarantee the environmental safety of the building. In addition, this material is relatively inexpensive and can be mounted without expensive equipment by anyone. It is desirable to choose the lightest varieties: they are not only more convenient for transportation, but also more effectively block the heat leaving to the outside. There are three key methods of work:
- wet
- dry;
- mixed
The dry method is practiced mainly in wooden buildings. Substance fall asleep in the intervals of lags or lighthouses, from above make a rough floor. At the bottom, the waterproofing is always laid out. Working in this way is easy and pleasant, the result is achieved quickly. Wet method involves mixing claydite with a typical concrete solution.
The insulation of the floors of baths with penoplex has become quite widespread. The technology of work has no special difficulties, moreover, it is quite accessible for any novice builder. Below you will have to put a substrate of sand and gravel, or make a concrete ceiling. However, Penoplex is ideal both on top of a draft wooden floor, and as one of the pieces of the “cake” of a warm floor. But it is impossible to lay the material on wet soil, it must dry thoroughly.
Bath floor is always equipped with a drain of water, and this fact can not be ignored when working on thermal insulation. Point drain drains of square or rectangular configuration differ in small size and can be put in any place. The slope for directing water to the gangway is at least 1%; this is important not to miss when designing a floor cake. The optimal solution is compacted extruded polystyrene foam.
Openings
Even when all surfaces in the bath keep heat stable, there is at least one problem area - the doorway. It is necessary to start the first frost or blow the winds, and omissions in its warming will respond to very serious consequences. To warm the canvas and not to overload it will help foamed polyethylene with an outer sheath of foil. By specific weight, it is comparable to paints and varnishes. The jamb is upholstered with either felt or more modern products, so long as they fit snugly to the surface and are soft to the touch, resistant to water.
Roof
Insulated ceiling, floor, doorway - very good. But there is one more channel of heat release, that is, a roof.Through it, a metal chimney pipe is usually removed, and steel, as is well known, “perfectly” contributes to the “withdrawal” of funds spent on heating to the outside. In the baths with cold attics or in the absence of an attic roofing slopes and planes are not insulated. But if there is a living attic at the top, there can be no two opinions - thermal insulation is obligatory.
The ceiling is insulated from the inside (from the steam room) with the help of metallized film materials. When laying fibrous heat protection, it should be blocked by a waterproofing membrane that conducts steam flow strictly in one direction. Flooring insulation (with laying boards and filling them with expanded clay) is carried out only on a wooden ceiling.
In this case, the load should be calculated so that it does not exceed the carrying capacity of the walls and floors.
System "warm floor"
To warm the floor in the bath, equipping it with heating circuits is quite a reasonable idea. Moreover, problems with getting hot water disappear by themselves. Such a measure is especially attractive when concrete is placed at the bottom, since it very quickly “draws out” heat. It is preferable to supply water to pipes made of polyethylene, steel alloys or metal-plastic. The spiral variant of laying the pipeline is simple and comfortable at the same time (the heat will evenly spread over the entire surface).
Tips and tricks
Thermal insulation of the bath is subject to the same laws as the insulation of the house. But elevated temperatures and high humidity make it possible to use far from all coatings suitable for ordinary rooms. Thus, among mineral wool, it is definitely not harmful to use only the latest modifications, which are combined with the help of biologically neutral acrylic. Peat blocks, filled with sawdust or straw, do not allow bacteria to develop, but absorb water. It is advisable to consider the option with cork mats - they are mechanically durable and not soaked with liquid, well stop the heat.
If the bath is insulated with natural materials, then it will be correct to treat them with special compounds that block the effects of insects, rodents and microorganisms. It is advisable to caulk log and logs with jute (flax). When they insulate a bath with brick walls, rolled and plate products are usually placed in a steel frame with a zinc profile.A layer of mineral insulation on logs and timber can be limited to 80 mm (if there is no danger of severe frost). In order for the insulator to retain its characteristics, it is taken 2-3 mm thinner than the cross section of the bars.
About how and what to insulate the bath, see the following video.