Heat-resistant adhesive: features and specifications
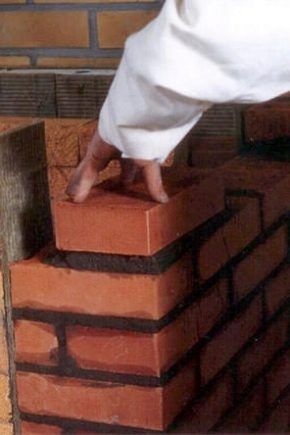
If necessary, connect surfaces exposed to high temperatures and an open flame, it is necessary to use heat-resistant adhesive. It can be universal, but more often it is necessary to choose the composition taking into account the material and the features of the operation of the bonded surfaces.
Special features
Heat-resistant adhesive is a fixing composition that can withstand significant temperature increases. This allows it to be used to create stoves and fireplaces, as well as industrial and engineering structures that are exposed to high temperature and are in direct contact with an open flame.
In addition to fire and heat resistance, such compositions exhibit high adhesion rates, as well as plasticity and stability. The latter properties determine the ease of use of the adhesive, as well as its relatively long viability.
Despite the variety of modifications of heat-resistant adhesives, all of them must meet the following requirements:
- resistance to high temperature exposure with further preservation of technical and operational characteristics;
- gas tightness;
- moisture resistance;
- resistance to linear expansion;
- good heat transfer performance;
- plasticity (determines the possibility of applying the composition in a thin layer);
- high adhesion;
- wear resistance and durability.
For many compounds, environmental performance and the ability to withstand low temperatures are also important.
Kinds and appointments
Depending on the resistance to high temperature exposure There are the following types of heat-resistant adhesives:
- heat resistant - this composition can withstand up to 3 hours of heating up to 140 degrees without loss of technical characteristics;
- heat resistant - withstands the same temperature, but for a longer time;
- heat resistant - withstands temperature effects in the range of -10 ... +140 degrees;
- heat-resistant, or heat-resistant - also called heat-resistant, withstands heating up to 1000 degrees;
- fire resistant (withstands not only an increase in temperature, but also contact with an open flame for up to 3 hours);
- refractory - similar in its fire-resistant qualities, but withstands this effect for an unlimited time.
Heat-resistant adhesive differs in composition, which, in turn, causes its differences depending on the method of application. So, there are compositions for working with furnace units and fireplaces (and here the differentiation of glue is also observed - for the base, for laying, for facing), options for outdoor (waterproof) and internal use. For fixing metal, glass, ceramics, specialized modifications of glue are also provided.
And for gluing dishes and repair kitchen utensils fit only heat-resistant food glues. Depending on the composition, the heat-resistant glue is divided into 2 large groups:
Natural origin
Basically, it has an aqueous solution of liquid glass or sodium silicate (which is why this glue has another name silicate).When mixed with chamotte filler, sand and mineral additives, it forms an environmentally safe adhesive that can withstand high temperature exposure up to 1200 degrees.
Acrylic glue is used in everyday life, but when it comes to single-component composition, it is not suitable for use on the street.
Synthetic based
The basis of this composition - oligomers, monomers and polymers, thereby achieving high refractoriness. For example, glue based on inorganic compounds can withstand up to over 1000 degrees, which is not the limit (there are compounds that can withstand up to 3000 degrees). In addition, these compounds are resistant to moisture, corrosive acidic environments.
Heat-resistant glue can be differentiated depending on the type of surface on which it is applied:
- For bricks. As a rule, we are talking about brick masonry stoves and fireplaces. The composition for these purposes must withstand heat up to 1000 degrees.
- For tile. Reinforced from the point of view of adhesion, the tile composition is used to fix the tile in the floor heating system, as well as when facing the furnace walls and the fireplace portal.
- Glue for metal. Available in the form of a viscous mass, similar in texture to the clay.It has another name - "cold welding", suitable for cast iron, stainless steel, aluminum, brass - all types of metals.
- Glue for glass. Usually used for fixing glass elements of electric, gas ovens and similar household appliances. When gluing electrical appliances, only the dielectric composition should be selected.
Separately, silicone heat-resistant sealant used to repair automotive systems should be highlighted. In addition to high temperature resistance, it demonstrates chemical inertness, moisture resistance and resistance to vibrations.
Composition
The main components of the composition are fillers, binders and plasticizers, which are taken in strictly measured proportions. Glue only requires water to be added to it, and attempts to “improve” the properties of the finished composition by introducing certain components into it themselves are meaningless.
The following elements can act as a heat-resistant base:
- Clay cement bindercombined with sand and chamotte filler. Shows high fire resistance, but has not the highest adhesion.On this basis, they usually make glue for stoves operating on solid fuels, and also use it in the repair of household heating appliances. Indicators of heat resistance are quite high - up to 1200 degrees. The disadvantage of this composition is that the bricks and elements to be glued must immediately be precisely laid on the right place. If you move a brick or tear it, then the adhesion, strength and gas-tightness of the stiffened seam will be significantly reduced.
- Aluminosilicate cement, kaolinfor which quartz sand acts as a filler, and liquid glass is used as a plasticizer. It has the best technical characteristics in comparison with the previous composition, however, it costs more. It shows the best adhesion, and the maximum heating temperature can reach 1360 degrees. Despite its good performance characteristics, aluminosilicate-based glue is usually used only as a lining compound for stoves and fireplaces. This is due to the fact that its service life does not exceed 20-25 years.
- Aluminosilicate cement, kaolin and quartz sand in combination talcchlorite flour as a plasticizer.Such a composition is characterized by versatility of use, increased weld strength and improved adhesion. Heat resistance reaches 1500 degrees. In addition, talc-chlorite flour converts hard thermal energy into soft infrared heat. It is logical that having such high characteristics, the honeycomb has a higher cost.
Description
Universal heat-resistant adhesive is a clear, viscous solution that has limited viability (on average, about an hour). Mounting masonry glue can have a different degree of plasticity, which makes it possible to produce seams of both standard thickness and application with a thinner layer.
If we talk about the compositions for fixing metal or ceramic surfaces, then it is a more dense and viscous substance. "Cold welding", rather, resembles clay.
Release form
Heat-resistant glue can be produced in dry or ready diluted form. If we are talking about a dry composition, it must be diluted with water in the proportions indicated by the manufacturer. It is better to knead the glue in small portions, since it has a small viability, after which it hardens.Ready-made compositions are often referred to as mastics, and are used by professionals. This is due to its higher viscosity and higher freezing rate. Without certain building skills, working with such compounds is not easy.
Masonry mixes are usually available in multi-layered kraft bags or plastic buckets of 5, 10, 15, 25 or 50 kg. Each manufacturer independently determines the nominal volume of packaged products.
If we are talking about a heat-resistant composition for metal, then it is liquid glue in small (from 50 mg) tubes or plastic sticks, as well as plastic buckets with a volume of several liters (the most common volume is 1.7 liters).
Choosing the form of release of glue and its volume, you should consider the nature of the work. In the open form, the glue quickly sets, so it is not rational to acquire a large amount of glue with a small front of work.
Manufacturers Overview
One of the best compositions based on aluminosilicate cement with talc-chlorite flour and quartz sand is considered universal. hot melt glue mixonit (Germany). The manufacturer indicates a number of tasks for which you can use this composition.However, in this list there is no indication of glue as a masonry one. At the same time Mixonit keeps the stove or fireplace laying well, however, it is not safe to use it in this way without the recommendation of the manufacturer.
If we talk about a more affordable domestic analogue of aluminosilicate glue, then this K-77. It withstands high and negative temperatures, the seam does not pass gases, it is moisture resistant. These properties make it not only the optimal masonry composition, but also glue for the base of the stove or fireplace.
Positive customer feedback also gets "Terrakotuperkamin", which is used as a masonry composition, and also fixes the facing terracotta tiles (for all other types of facing tiles, the composition is not suitable). The tile should be laid on this clay-cement with chamotte filler composition follows in rows, giving time for the glue to set after each 2-4 belt. An option is also suitable for masonry stoves. "Plitonit SuperFireplace Ogneupor".
For metal and glass elements of fireplace designs will need a special glue. Heat-resistant metal compounds are represented by the product. "Dow Corning Q3-1566" and red glue-sealant from Belife Silicone . The first one withstands heating up to 350 degrees, retains high performance properties and durability in room conditions, is gas-tight, moisture-resistant.
For finishing the external walls of the stove or fireplace portal glue for high temperatures "Profix". It demonstrates a harmonious ratio of cost and quality, can withstand temperatures up to 1200 degrees. Due to the possibility of applying a thin layer, the lining looks neat and the glue consumption is noticeably reduced. Popular is another composition for finishing - "Geresit Flex CM 16", the main advantage of which is the possibility of facing even the uneven surface of the masonry.
Glue-sealant is suitable for operation in the range of -70 ... +300 degrees, it should be applied at a temperature not lower than +18. In assortment "Plitonite" You can also find a compound for metal - "Premium +1500". It is a heat-resistant composition for bonding metal, ceramics, glass, including with each other.
Among domestic manufacturers of heat-resistant compositions should be distinguished company "Diola". Heat-resistant adhesive D-314 is designed for lining fireplaces and stoves with ceramic tiles and can withstand heating up to 850 degrees.The tile is securely fixed, and if necessary, its location can be easily adjusted until it hardens.
Another finishing compound (which, by the way, is also suitable for masonry) is GM-215 glue from Russian manufacturer "Hercules". The heating temperature reaches 1200 degrees, can fix low-porous ceramic and glazed tiles. The lack of glue is its increased rigidity, which is why in the process of gluing tiles can not be moved. If it is nevertheless necessary, then you should remove the previously applied layer of glue and put a new portion of it.
Fire resistant option for gluing glass surfaces can be glue "UHU Glas". It can heat up to 125 degrees, has a high setting speed, resistance to UV exposure.
For ceramics you can use Cyanoacrylate-based glue “UHU Porzellan Keramik”. The adhesive is characterized by good ductility, high adhesion and strength, but only when gluing small areas.
How to use?
If you are planning to do the laying or lining of the fireplace with your own hands, choose dry mixes. It's easier to work with them.Before applying the adhesive, it is necessary to moisten the working surfaces, and soak the bricks in water. For clay, the residence time in the liquid is about 10-15 minutes, for refractory it should not exceed 10 seconds.
The working base should be carefully prepared - remove dust, grease, paint residues or whitewash. The presence of any coatings and dust reduces the adhesion of hot melt.
Glue is applied with a thin uniform layer, the recommended thickness of the seam - no more than 10 mm.
Professional Tips
When choosing a heat-resistant glue in the first place should be considered the scope of its application. Even the most high-quality and expensive composition, being not in "its" place, will not demonstrate the stated high performance. Thus, a thermally conductive glue is recommended for fireplaces, however, it has high thermal conductivity. In this case, the seams formed must be impermeable and moisture-resistant.
Increased water resistance, chemical inertness, and most importantly - resistance to the influence of not only high, but also negative temperatures should demonstrate the mixture for the bases of the furnace. When facing, in addition to heat resistance, in the first place are indicators of adhesion.They should be as high as possible, since the adhesion strength of the tile largely depends on this. High-quality composition allows you to mount tiles in any direction, including the bottom up.
Heat-resistant glue for fireplaces and stoves should be applied with a thin layer. If there is a slight surface irregularity, then it is acceptable to apply a thicker layer at certain points. This will level the height differences.
In the next video you will find a review of heat-resistant single-component transparent adhesive sealant Kafuter K-705.